Production System
The manufacturing program is one of the most powerful solutions offered by AccFlex to cover the industrial sectors, providing advanced tools to serve industrial companies of various specialties. The factory management program offers a sophisticated workflow for managing production operations, starting from production planning and tracking the stages of product manufacturing to the completion and delivery of products. It also provides a strong foundation for accounting for both direct and indirect industrial costs.
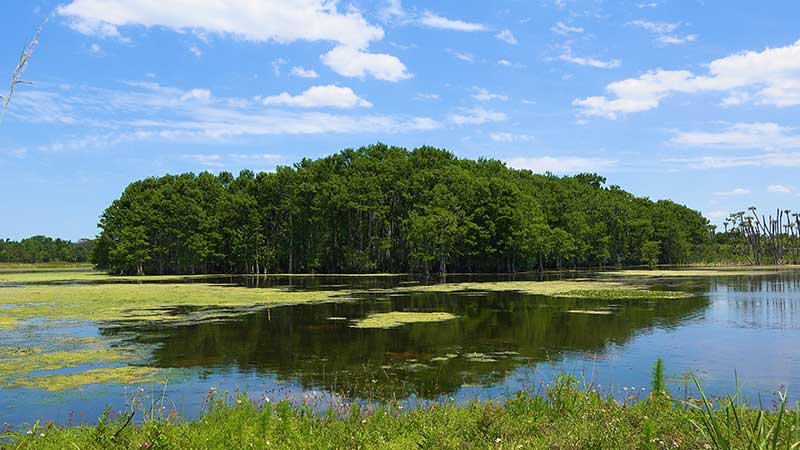
Factory Management Program Screens
Production Planning:
The Production Planning screen is an essential tool for production departments within factories. It enables users to create production plans at the level of final products. The system automatically provides key indicators and information that help the production manager or relevant departments in planning, such as daily sales or withdrawal rates of products.
Production Orders:
Production managers can manage and execute production orders with great flexibility and ease. Production orders can be carried out based on issued sales orders or direct operations. The production manager can control the level of detail entered into the system according to work requirements, such as planning the order, specifying the expected time to complete the operations, and other details. Ultimately, the system manages the actual withdrawal of raw materials, the actual production of the finished product, and production waste or defects.
Cost Measurement:
Accurately determining and measuring costs is one of the key features of the production system. The system allows users to automatically calculate direct costs such as raw materials and labor costs, as well as indirect costs and production machinery costs with high precision. This leads to an accurate determination of inventory costs and the cost of goods sold. Costs can be measured at each stage of production.
Operation Monitoring:
The Operation Monitoring screen allows users to track production operations, whether completed or planned. Production managers can monitor the completion level of product production by tracking the completion of sub-stages and identifying the remaining stages at the product level. It also allows tracking the productivity of work and machinery.
Machine Data Recording:
Machine and production equipment data are recorded for comprehensive tracking. Detailed information such as model, warranty, last maintenance date, expected maintenance date, and other important data are also recorded.
Reports of the Factory Accounting and Production Management Program
- Incomplete Manufacturing Movements Report During the production process, quantities are withdrawn from the raw materials warehouse and added to the finished goods warehouse. Errors may occur where quantities are withdrawn from the raw materials warehouse without being added to the finished goods warehouse, causing production issues. The Incomplete Manufacturing Movements Report allows you to review all incomplete manufacturing operations and complete them as necessary.
- Production Order Details Report This report displays all details of the manufacturing operations for a specific production order, including movement code, serial number, or date. It shows all executed final product items during the production order, the executed quantity, quantities withdrawn from the raw materials warehouse, and quantities added to the finished goods warehouse.
- The Best Accounting Program for Factories and Cost Accounting
Customized Systems to Serve Industrial Company Departments
Financial Management:
The AccFlex accounting program for factories is one of the best accounting programs for factories, meeting the financial management requirements of various factories. The system provides a comprehensive documentation and financial cycle that aligns with industrial companies, starting from the availability of raw materials to the completion of manufacturing. It also offers automatic translation of financial transactions into daily journal entries and provides a thorough analysis of all product cost elements, whether direct or indirect, providing a strong basis for accurate product pricing and profitability analysis.
Production Management:
The AccFlex system supports production departments within the factory at various stages of their work. It enables users to design a factory management program that meets the factory's requirements and the nature of the product, including setting product specifications, standard components, various production paths, and managing production machines and equipment. It also supports various operational processes such as production planning, work orders, and monitoring the production process.
Procurement and Inventory Management:
The procurement management system in the AccFlex suite for industrial companies is an essential part of the integrated solutions for managing industrial companies. This system provides a complete documentation cycle that adheres to best practices in procurement management, ensuring that the production departments' needs are met efficiently and on time. The documentation cycle includes various forms such as material requests, purchase requests, quotation comparisons, purchase orders, receipts, and inventory transfers. These processes help achieve a balance between costs and ensure that necessary resources are provided in an organized and efficient manner.
Sales Management:
The sales system in AccFlex is interconnected with other relevant departments due to the interconnected work cycle, whether in terms of sales planning, which the production department uses to make production planning decisions, or supporting some industries, especially non-standard production. In such cases, the sales department first records customer orders and product specifications, and then production is carried out according to the customer's specifications. The system also allows the sales department to track the progress or completion of products fully.
Human Resources Management:
AccFlex offers an integrated human resources system that serves manufacturing companies in several important aspects, such as linking labor to production orders, thus determining the exact cost of products from the wage element based on the hourly wage rates derived from employee salaries in the HR system. It also allows linking labor to production plans as a type of planning.
